Диффузия различных металлов в алюминии изучена достаточно подробно, однако диффузионные перемещения атомов легирующих элементов в многокомпонентных сплавах происходят по более сложным законам.
Время выдержки при температуре закалки, необходимое для растворения интерметаллидных фаз, зависит от структурного состояния сплава, типа печи и толщины изделия.
На кинетику процессов, происходящих при нагреве под закалку, существенное влияние, кроме фазового состава, оказывает структурное состояние — степень проработки структуры; форма, размер, внутреннее строение зерен и их расположение относительно осей деформации; размер и распределение интерметаллидов; тип и плотность дефектов кристаллической решетки. Структурное состояние в полуфабрикатах и деталях перед закалкой определяется видом и условиями предшествующих обработок.
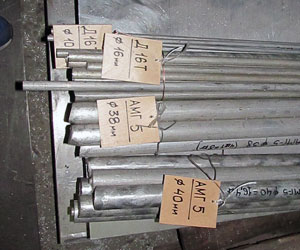
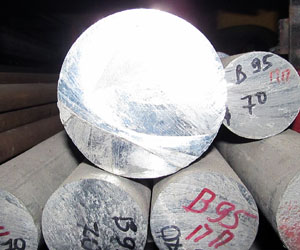
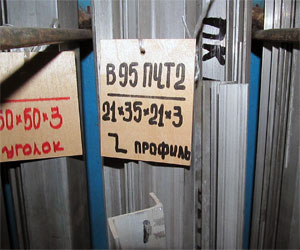
В изделиях, подвергавшихся пластической деформации, при нагреве наряду с процессом растворения избыточных фаз протекает процесс рекристаллизации. Величина рекристаллизованного зерна в основном зависит от степени и скорости деформации, длительности нагрева до заданной температуры и выдержки при ней. В результате длительного нагрева прессованных полуфабрикатов может произойти частичное или полное снятие эффекта структурного упрочнения и рост зерна, что приведет к снижению прочности в долевом направлении. Это следует учитывать при выборе длительности выдержки нагрева под закалку.
В холоднодеформированных полуфабрикатах, характеризующихся главным образом ячеистой структурой, плотность дислокаций выше и диффузионные процессы растворения избыточных фаз при нагреве под закалку идут значительно быстрей, чем в горяче-деформированных полуфабрикатах с полигонизованной и, особенно, с рекристаллизованной структурой. Поэтому для холодно-деформированного металла требуются более короткие выдержки при закалочной температуре.
Большими скоростями диффузии легирующих элементов и наиболее короткими выдержками при нагреве под закалку отличаются сплавы, полученные из порошковой заготовки.
В процессе производства порошков при распылении достигается высокая скорость кристаллизации и охлаждения сплава, что способствует увеличению степени пересыщения твердого раствора легирующими элементами и вакансиями, повышению дисперсности частиц первичных интерметаллических соединений и измельчению микроструктуры . Все эти факторы сохраняют наследственное влияние на диффузионные процессы в полуфабрикатах.
На скорость процесса перевода атомов легирующих элементов в твердый раствор оказывает влияние предыдущая термическая обработка. Предшествующая закалка, переведя основное количество легирующих элементов в твердый раствор, обеспечивает их более равномерное и дисперсное распределение при последующем старении. В связи с этим процесс растворения при повторном нагреве под закалку протекает более быстро и выдержка в случае перезакалки может быть значительно сокращена
Предшествующий отжиг, огрубляя продукты распада и приводя сплав в более равновесное состояние, как правило, существенно замедляет процесс растворения избыточных фаз по сравнению с деформированным состоянием. Поэтому для сплавов в отожженном состоянии требуется большая выдержка при последующем нагреве под закалку.
Особое внимание следует обращать на длительность выдержки плакированных листов при закалочных температурах. С повышением температуры и увеличением длительности нагрева возрастает скорость и глубина диффузии легирующих элементов сплава в плакирующии слои . В случае сквозной диффузии в этот слой коррозионная стойкость резко снижается.
Детали из плакированных листов, особенно тонких, не рекомендуется подвергать многократным закалкам вместо отжига при гибке, выколотке и других операциях.
Длительность нагрева 15 мин при 500 °С вызывает диффузию меди в плакирующий слой на такую же глубину, как и нагрев в течение 1 ч при 350 °С, что может привести к сквозной диффузии на тонких листах. Для плакированных листов толщиной более 3 мм рекомендуется проводить в случае необходимости не более двух повторных термообработок, для толщины 0,5—3,0 мм — не более одной и при толщине менее 0,5 мм повторная термообработка не рекомендуется .
На общую продолжительность пребывания садки металла в термическом агрегате оказывает влияние скорость нагрева до заданной температуры, которая определяется типом теплоносителя и скоростью его циркуляции, видом теплопередачи, массой садки и величиной поверхности нагреваемых изделий, мощностью нагревателей и конструктивными особенностями термического агрегата.
В настоящее время для нагрева под закалку наиболее широко применяют электрические печи с принудительной циркуляцией атмосферы, рециркуляционные печи типа ПАП и селитровые ванны. Наибольшую скорость нагрева металла обеспечивает селитровая ванна. В печах с воздушной атмосферой тепло лередается преимущественно за счет конвекции, и интенсивность теплопередачи во многом определяется скоростью циркуляции воздуха . Для листовых материалов наиболее эффективен струйный нагрев, при котором нагретый воздух в виде высокоскоростных струй направляется на нагреваемое изделие. Коэффициент теплоотдачи в печах с указанным способом нагрева в 3—4 раза выше, чем в печах со сплошным потоком воздуха. Скорость нагрева в определенных пределах можно варьировать массой и плотностью садки.

Учитывая, что длительный нагрев до заданной температуры может привести к значительной глубине диффузии в плакирующий слой, росту зерна и частичной или даже полной потере эффекта структурного упрочнения, рекомендуется продолжительность нагрева до начала отсчета выдержки ограничить 0,5—1 ч для плакированных полуфабрикатов и 1—3 ч — для неплакированных.
Листы, прутки, плиты, полосы толщиной 0,5—150 мм при нагреве в селитровых ваннах выдерживают[4] 10—80 мин, а при нагреве в наиболее широко применяемых для этой цели электропечах с принудительной циркуляцией воздуха 30—210 мин. Выдержка фасонных отливок при температуре закалки более длительная (2—15 ч); за это время растворяются грубые выделения интерметаллидных фаз . Скорость охлаждения при закалке должна быть выше критической, под которой понимают наименьшую скорость охлаждения, не вызывающую распад твердого раствора. Охлаждение деформированных сплавов после закалки проводят в холодной воде, а фасонных отливок в подогретой воде (50—100 °С) во избежание их коробления и образования трещин.